PVDF (Polyvinylidene fluoride)
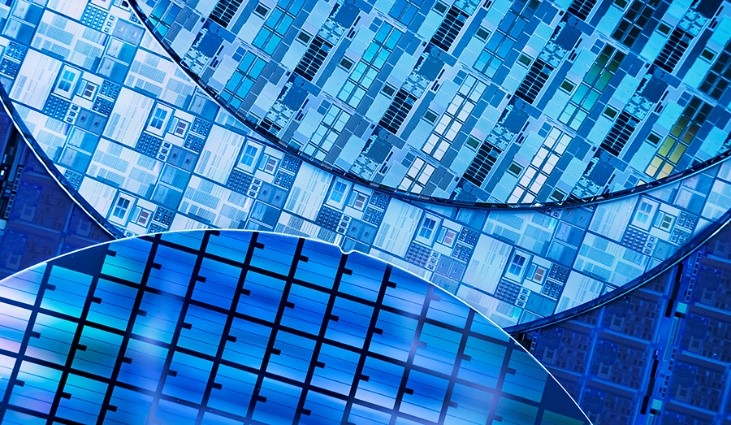
Product description
PVDF stands for Polyvinylidene fluoride and is a polymer resin product in which some of the hydrogen atoms are replaced with fluorine atoms in the molecular structure of polyethylene, and at the same time has the advantage of general fluoride resin, it has lower specific gravity and lower melting point than PTFE products, so it has high processability and good mechanical properties. Among fluoride resins, it has strong toughness, low coefficient of friction, strong corrosion resistance, aging resistance, weather resistance, and excellent radiation resistance.
Basic information
Data
PVDF
Type Condition
Dry: The original package does not need to be dried.
Injection temperature
180~230℃
Mold (Type) temperature
60~90℃
Extrusion temperature
180~265℃
Die head
66~140℃
APPLICATIONS
- Pipes and Valves
- Electrical wires for insulation
- Printed circuit board
- Composite electrodes for lithium-ion batteries
- Biomedical devices
Separators

Product description
Separators are an integral part of the performance, safety, and cost of lithium batteries.
A separator is a thin insulating membrane, and has about four features.
Separators separate cathode and anode to prevent contacts of them inside a battery.
Separators have submicron sized pores that works as channels where lithium-ions move between cathode and anode.
Separators have high mechanical strength, so they prevent by-products or foreign substances from coming in to ensure safety.
Basic information
- A wet separator is suitable for processes with a high number of flying sparks, and for the extraction of explosive, sticky, damp and flammable dusts. Typical processes include grinding, polishing, deburring, sawing, cutting, transferring and mixing. Wet separators are available as mobile as well as stationary units.
- A dry separator is suitable for work processes such as grinding, polishing, deburring, welding, soldering, laser cutting, sawing, separating, transfer and mixing.
High-molecular materials with high insulation such as polyolefin, polypropylene are used for separators. These materials are stretched to make tiny pores, and there are dry and wet processes to do it.
Function: Used in separating lithium ion battery cathode and anode,to prevent short circuit.
he battery separator includes a microporous co-extrusion membrane that has at least two layers made of extrudable polymers.
(used in mobile phones, laptops, and other devices that require light, rechargeable power)
Aluminium hydroxide
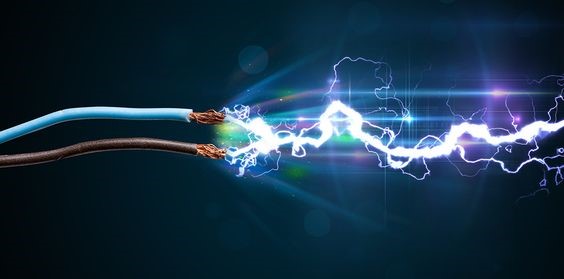
Product description
Aluminum hydroxide, Formula aluminium hydroxide, Al(OH)3, ATH)
Aluminum hydroxide is the most widely used inorganic flame retardant additive.
Basic information
It is a basic inorganic chemical product with excellent chemical heat resistance, transparency, and particularly flame retardancy. It is a product that dries general aluminum hydroxide products (containing about 9-10% moisture) with hot air within 130℃. Aluminum oxide is the industry standard for battery separator coatings, providing a wide range of benefits for battery safety, durability and performance.
Alumina brings benefits to your battery separators by:
Thermal conductivity
Insulation
Durability
Common Applications
- cable insulation materials
- Display materials
- data networks
- coatings for electric wires
- Semiconductor processing materials
Spherical magnesium oxide
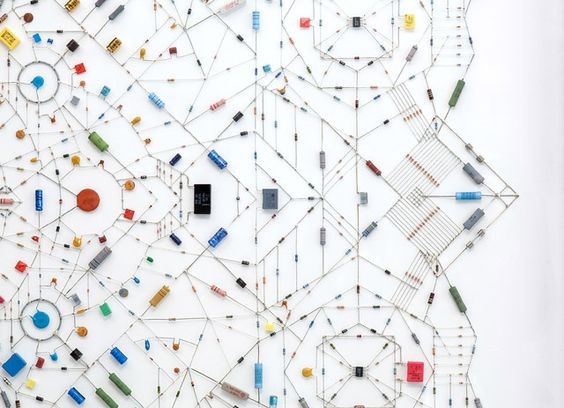
Product description
Magnesium oxide (MgO), or magnesia, is a white, hygroscopic solid mineral that naturally occurs as a periclase and is a source of magnesium.
Basic information
Magnesium oxide (formula: MgO) is magnesium oxide, an ionic compound. It is a white solid at room temperature.
Magnesium oxide exists in nature in the form of magnesite and is the raw material for magnesium smelting.
Insulation with high fire resistance. It can be converted into crystal by high temperature firing above 1000℃ and turn into burnt magnesium oxide (also known as magnesia) or sintered magnesium oxide at 1500~2000°C.
Spherical magnesium oxide is used in electronic materials, packaging insulation material, catalysts, polymer materials, transformer steel, insulators, industrial cables.
The spherical magnesium oxide of the present invention has the advantages of high sphericity, excellent filling property even when filled in a resin, a smooth surface, and high moisture resistance.
High purity atomized spherical magnesium powder is manufacturing by the centrifugal atomization technology that is melting minimum 99.8% purity magnesium and spraying the molten metal under the protection of an inert atmosphere.
High purity atomized spherical magnesium powder is known with the outstanding features of high apparent density, high content of active magnesium, high fluidity, high stability, small particle size and small specific surface, and so on.
Common Applications
- Electronic components
- LED lamp
- Electrical vehicle
- Required characteristics
- Thermal Conductivity
- Electrical insulation
Magnesium hydroxide
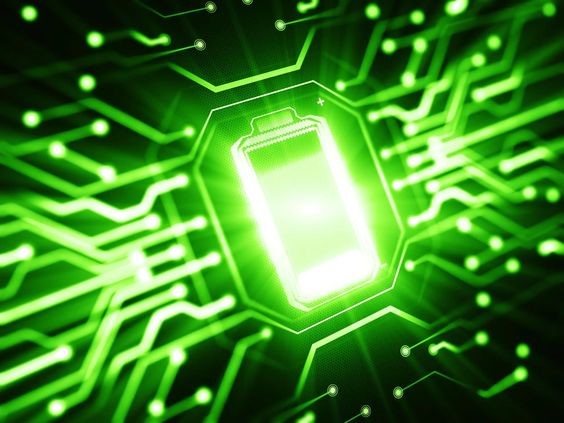
Product description
Magnesium hydroxide is a weakly basic ionic bonding material. Magnesium hydroxide has a very low
solubility in water, so when mixed with water, the solution becomes supersaturated, giving it a white color similar to milk. For this reason, it is nicknamed ‘Magnesia milk’.
Basic information
Magnesium hydroxide is widely used in electronic devices, laser technology, and batteries. For the production of rechargeable batteries, also used to produce flame retardant magnesium hydroxide for cable sheath, partition, electronic equipment sheath and etc.
Magnesium hydroxide is added to modify or improve the characteristics or properties of an individual layer or the separator as a whole.
Common Applications
- Electrical vehicles
- cable sheath
- electronic devices
- rechargeable batteries
Laminated type battery